In the fast-paced world of warehousing, efficiency is key. Whether you're dealing with large-scale operations or managing a smaller setup, optimizing your fulfillment process can make a world of difference. We've compiled a list of quick hacks that will help streamline your operations, save time, and boost productivity.
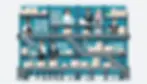
1. Streamline Your Picking Process
Implementing an effective picking process can significantly reduce fulfillment times and errors. Consider options like zone picking or batch picking to minimize travel time and increase speed.
Zone picking divides the warehouse into different zones, with pickers assigned to each specific area, thereby reducing unnecessary movement. Although intuitive, it's crucial to regularly review the configuration of your zones to ensure items most often sold together are located near each other, reducing travel time and enhancing worker productivity. On the other hand, batch picking allows workers to pick multiple orders simultaneously, reducing trips back and forth from the picking area.
For more nuanced techniques in picking processes, like directed picking paths that further cut down errors by segmenting paths logically, consider resources such as smart warehousing techniques to guide implementation and increase your operation's efficacy.
2. Use Technology for Inventory Management
Leverage technology such as RFID tags and real-time tracking systems to keep a tight grip on inventory levels, reducing mistakes and enhancing accuracy.
Integrating RFID technology can significantly enhance inventory control by providing real-time data on every product's location within the warehouse. Such transparency allows you to maintain optimal stock levels and mitigate the common pitfall of overstocking or stockouts. Similarly, real-time tracking systems can alert staff when stock is running low, helping prevent critical delays. For businesses expanding into multiple geographic regions, these systems support efficient capacity management.
Utilizing a robust warehouse management system (WMS) increases the precision of your operations and helps align inventory with demand forecasts as detailed in smart warehousing FAQs which are essential reads for scalability insights.
Centralizing inventory data platforms ensures an accurate reflection across various points in the supply chain. Such technologies not only streamline operations but lead to strategic insights guiding future inventory decision-making.
3. Optimize Warehouse Layout
Arrange your warehouse strategically for smoother operations. Ensure high-demand products are easily accessible and consider implementing a just-in-time stocking system.
An optimized warehouse layout is a game-changer for efficiency. Start by conducting a thorough analysis of movement patterns and item displays. High-demand products should be placed at easily accessible points to decrease picking time. A well-planned layout takes advantage of vertical space, using racks and shelving systems which free up floor space for high-traffic workflow.
Furthermore, consider the implementation of a just-in-time stocking system. This limits inventory levels inside warehouse grounds and promotes a continuous flow of goods. The impact of this can be profound, as seen in recent trends surrounding warehouse digitization which offer substantial improvements in logistics and cost-effectiveness for e-commerce ventures.
4. Enhance Communication Channels
Improving communication among team members can lead to quicker problem-solving and more efficient operations. Consider using instant messaging apps or radio systems for better connectivity.
Instant messaging platforms designed for operational environments allow staff to stay connected in real-time, ensuring rapid response to any issues that arise. With designated channels for each department, you ensure clarity and prevent the possibility of crossed wires.
Radio systems can complement digitized solutions, especially in noisy environments where text communication might not suffice. Clear communication systems are essential for operational fluidity and avoiding warehouse blind spots.
Improved communication translates into quicker adjustments and stress-free problem-solving. These enhancements directly affect the fulfillment chain by reducing potential backlogs.
5. Regularly Train Staff
Conduct regular training sessions to keep staff updated on the best practices and new technologies. This ensures everyone is aligned and capable of handling their tasks efficiently.
Training keeps your team adept and comfortable with emerging technologies that inevitably influence daily tasks. Regular sessions of technology updates, coupled with assessments, maintain a knowledgeable workforce ready for systems transitions, such as those seen in recent fulfillment practices.
It’s also imperative to stress the importance of soft skills in team operations, like conflict resolution and time management. Together with technical proficiency, these cultivation efforts weave a strong fabric for operational success, greatly aiding in achieving strategic efficiency goals.
6. Automate Repetitive Tasks
Automation can drastically cut down time spent on repetitive tasks. Utilize conveyor belts, automated sorting systems, and robotics to enhance speed and accuracy.
Automation in warehousing has transformed the traditional landscape into a nuanced and dynamic environment. By adopting modern applications such as automated guided vehicles (AGVs) and robotic picking, time and labor efficiency grows remarkably. These advances, along with RFID systems, pave the path for swift adjustments in processes.
Conveyor belts take automation further by seamlessly incorporating into existing systems, elevating productivity while optimizing worker roles. Automating tasks translates to fewer errors and frees up valuable resources to focus on critical areas like client relations and growth efforts.
7. Embrace Lean Warehousing Principles
Adopt lean warehousing practices to minimize waste, streamline processes, and improve overall efficiency, focusing on value-adding activities.
Lean warehousing is about embracing methods that cut down on excesses while amplifying processes that generate value. The 5S methodology (Sort, Set in Order, Shine, Standardize, Sustain) originates from lean principles and when applied systematically, can escalate warehouse productivity.
The focus is to eliminate waste across all areas by emphasizing continuous improvement and empowering every team member to take initiative in identifying and solving inefficiencies.
With this approach, not only is inventory handled more efficiently but the entire supply chain can be recalibrated for maximum renewal, reinforcing even those processes that are already functioning seamlessly.
8. Prioritize Safety Measures
Maintaining safety standards not only protects staff but ensures smooth operations. Implement regular safety checks and provide necessary safety gear to all workers.
A safe warehouse environment is crucial for sustaining seamless operations. Regular audits and strict adherence to safety protocols prevent accidents which can lead to downtime, thereby hindering productivity.
Promote a culture of safety by organizing workshops, displaying clear signage, and employing technology like AI monitoring systems to ensure that compliance is integrated into daily routines.
9. Implement Energy-Efficient Practices
Opt for energy-efficient lighting and equipment to reduce costs and promote sustainability, creating a green warehouse environment.
Switching to LED lighting and efficient HVAC systems, combined with equipment that uses renewable energy sources, results in a significant reduction of operational overheads. Furthermore, exploring energy recuperation methods can turn your warehouse into a self-sustaining or even energy-producing facility.
Sustainable practices not only curtail costs but possess the profound advantage of aligning operations with environmentally conscious ideals, tapping into the market segments that prioritize green practices.
10. Utilize Data Analytics for Better Decisions
Leverage data analytics to gain insights into warehouse operations, helping you make informed decisions that enhance efficiency and productivity.
Harnessing data analytics opens up a world of opportunities for pinpointing inefficiencies and crafting more accurate demand forecasts. Technologies, such as predictive analytics and machine learning, can analyze complex data sets to reveal patterns in customer behavior, informing inventory procurement and workforce distribution.
Further integrating your warehouse management systems with business analytics tools ensures a broader oversight, allowing tailored strategies that are data-driven and results-oriented.